I found an experienced blower builder just a few hours from where I live who quoted me a better price for a complete 6-71 blower"kit" than that of the popular builders, and figured I'd save some extra coin picking it up in person rather than shipping a hunk of aluminum and steel cross country. For an additiional $400 I could have gotten a polished case but chose the natural satin (as-cast) finish with plans to paint it with black wrinkle. This would be in keeping with the 'no-bling' theme of the car and it's black accents.
As it turned out, he was a Chevy guy with a little less experience with Mopars than he claimed. I'll elaborate as I go but suffice it to say that if I had to do all this again, it would have been better to deal with Dyers, Hampton or even BDS directly in the first place.
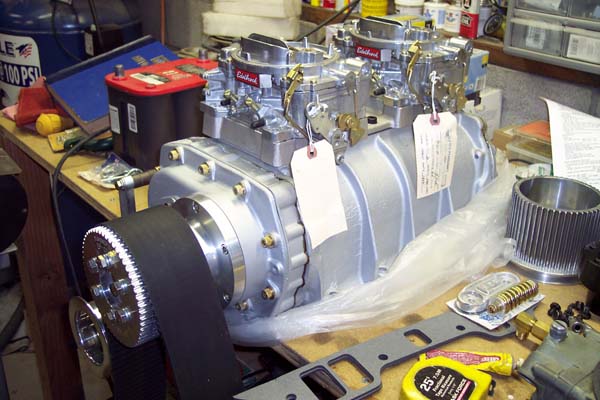
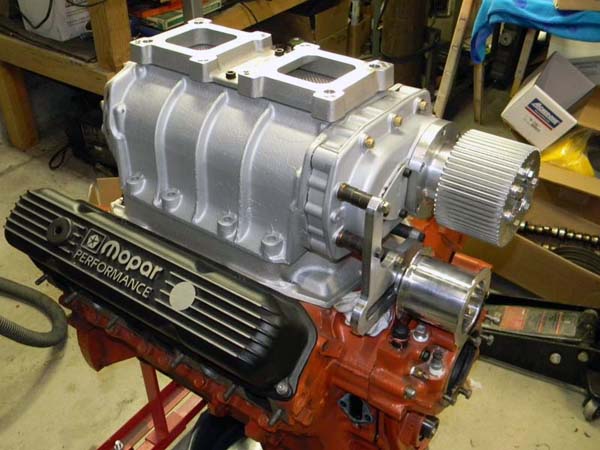
While the "new" block and bottom end were at the machinist I used the old, cracked long block as a platform to mock up the blower and drive setup. Space would be at a premium between the drive and radiator - space is tight without a blower on a BB A-body! Now was the time to work everything out - not after the engine is in the car.
BDS recommended and sent him their 5.75" snout and coupler, some pulley spacers, and a swing-arm idler bracket. (The spacer for the idler pulley was missing... sigh)
Their longer snout would have been nice because I would not have had to run the upper pulley in the outboard (open end out) position - which is not a big deal, mostly a looks thing. But a longer snout is even more money.
In this picture I'm aligning everything for a 2V pulley system - that is, an alternator/WP pulley and a power steering pulley. Later, I did away with power steering so that I could eliminate one of the accessory V pulley's and gain more clearance between the blower drive and radiator.
For me, pulley alignment centers around the water pump because that's the one pulley you can't easily move closer to the engine. So any spacers required to bring the upper and lower drive pulley's into alignment, along with the idler are based on WP pulley position. Of course, if you choose to run an electric water pump, then the requirements might be different. Same with alternator location. I wanted to keep things simple with a water pump and alternator in their stock locations.
On the fuel delivery side I reused the Carter street/strip mechanical pump from the original build which should have no trouble keeping the Edelbrock carbs from running dry. While an electric fuel pump might be a good idea on a drag car, I didn't feel it was necessary here - just simple, reliable, quiet.
An off-the-shelf Edelbrock/Russell "ProClassic" black hose runs from the pump up through an inline filter before entering a pressure regulator. It exits the regulator and is split in a 'Y' block that feeds the carbs. The cost of AN fittings, adaptors, hose ends, etc. can add up quickly. I used less costly Summit Racing brand black fittings where possible.
Carter/Edlebrock carbs are sensitive to fuel pressure with 5-5.5 psi the recommended max feed pressure. I preset the regulator on the bench to 5.5 psi using compressed air and gauges. Too much pressure and you'll overpower the needle/seat and it'll flood.
6-71 on the bench, fresh from the builder. Threw a pair of carbs on for the picture.
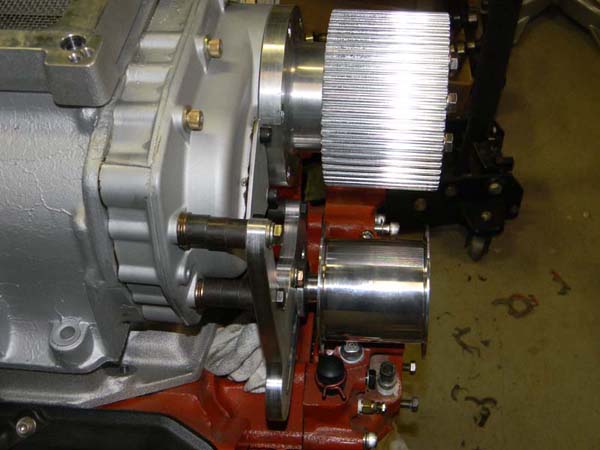
Oh, boy. Here we go....
You'll notice right away that the drive pulley and belt idler are nowhere near where they should be. Even with the drive pulley flipped to an outboard position it would still come up an inch or more short for drive belt clearance. You can only use so many pulley spacers - and it just looks dumb.
The builder had installed and sold me the wrong drive snout and idler system. (His spacer system for the idler bracket was pretty hokey too).
The snout, coupler, and idler bracket all had to be returned for the right parts. And with that, the original price quote went out the window because the correct parts cost more money. There went the money I'd saved dealing with him - and then some.
He gets a lot of his parts from BDS (Blower Drive Service) in CA. Why he didn't consult with them about the correct parts in the beginning is a mystery, and it would ultimately take another month to get the right parts back.
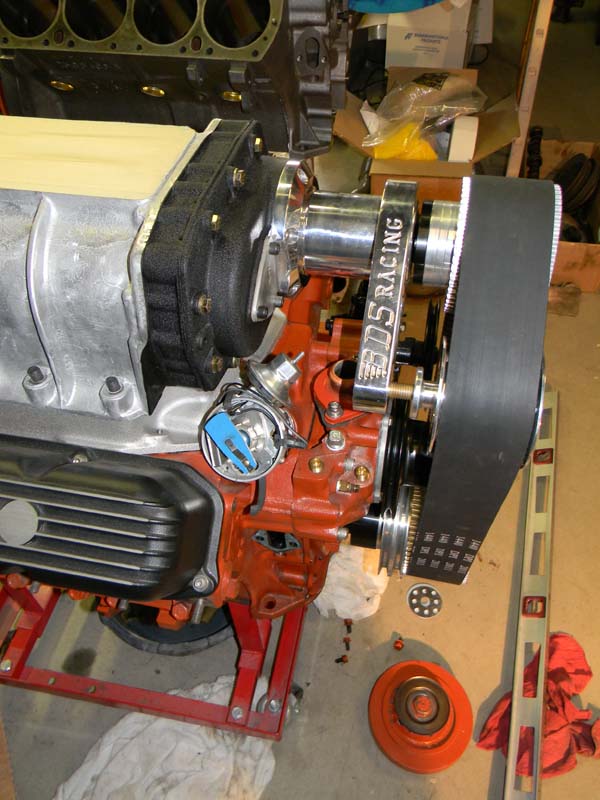
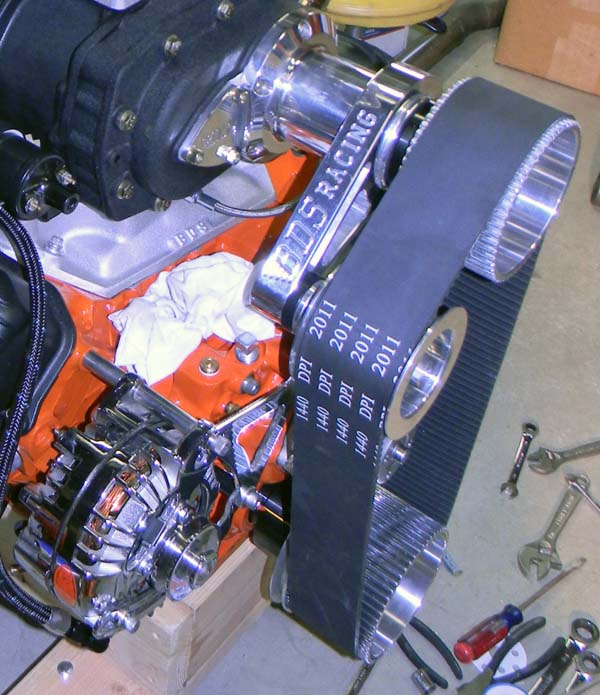
A great source for blower parts and accessories is Good Vibrations Motorsports in CA. Their prices are right and service/shipping is fast! I picked up a number of spacers and other odds and ends from them - most were BDS products.
Assuming you run a blower crank hub and not an aftermarket balancer, and a single v-belt off the crank (alternator/wp), here's what you'll need starting at the bottom:
Crank hub, .300" pulley spacer, 1 V-pulley, Drive Pulley
1/16" shim (Moroso) under stock WP pulley. This will fine tune the alignment of the WP pulley to the crank pulley.
5.75" snout and coupler, .300" pulley spacer, Drive Pulley, Swing Idler Arm, .400" idler pulley spacer, Idler Pulley with bearing, standoff, etc.
Of course you'll need the correct length drive pulley bolts, idler pulley bolt (trim to length) and a longer 3/4"-16 crank bolt (grade 9) with thick hardened washer of the correct diameter for the register. I believe that bolt was 3.5" long. I found the bolt locally but you can spend big money and order a chrome moly piece if you feel the necessity. Not needed for my application.
With this setup, the stock alternator brackets will work and everything will line up while keeping everything as close to the engine as possible.
Now, if you're installing an 8-71 blower, all bets are off on my parts list because the case is slightly longer.
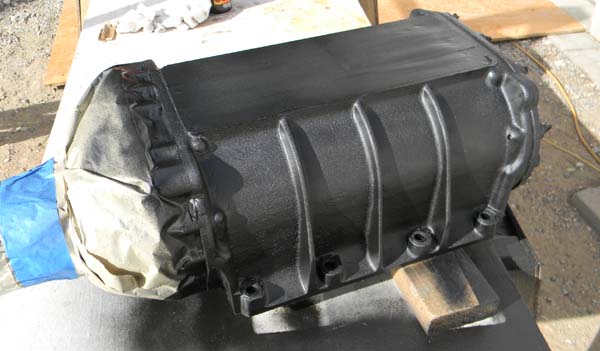
While waiting for parts, the case was masked and sprayed with VHT Black Wrinkle finish paint.
Final mockup of the blower drive, throttle linkage, and fuel plumbing took place on the fully assembled long block.
On the original build I used a 727 kickdown kit from Bouchillon Performance which employs a cable rather than linkage to control throttle pressure at the trans. Their system works perfectly and I wanted to reuse as much of this as possible. The initial plan was to mount the kickdown brackets and cable at the carb just like they are in a normally aspirated setup along with a simple dual carb linkage. I determined this might cause interference issues so I had no choice but to move everything back down near the intake.
The blown dual carb (inline) blower linkage kit, once again, came from Good Vibrations Motorsports. I then made some aluminum brackets and tabs to create the mounting points for the throttle and kickdown cable and still get all the geometry right.
Chrysler Throttle Cable Clamp
Chrysler Throttle Cable
Stud and Clevis
Bouchillon Kickdown
Cable Stud
Bouchillon Kickdown
Cable Bracket
Everything is fully adjustable and it doesn't take a lot to get everything working in a very precise fashion.
The only thing left to add is a throttle return spring which I did by fabbing a tab (not pictured) for one of the carb mounting studs and running a spring between it and the hole at the bottom of the throttle lever on the front carb.
I fabbed a bracket that attaches to a blower/manifold stud and holds the pressure regulator and distribution block firmly in place.
A port on the distribution block feeds an external fuel pressure gauge.
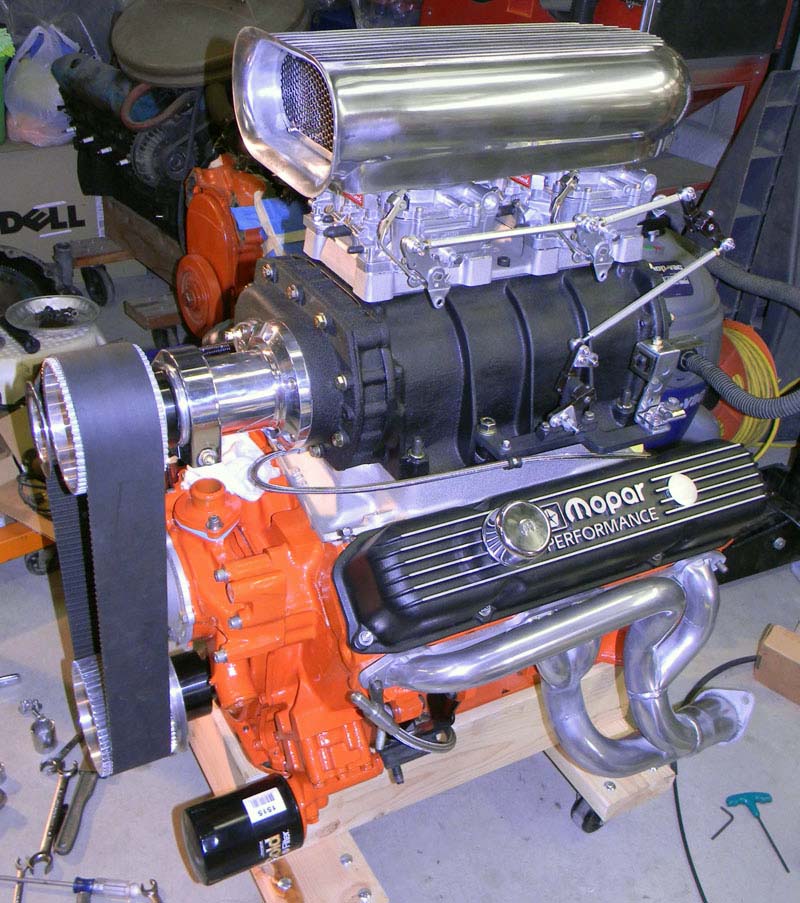
The Milodon braided dip stick and Schumacher headers were carried over from the original build. Don't forget a quality "Wix" made oil filter from Napa. It'll be a little roomier on this side without the power steering pump.
The blower builder apparently did not take engine displacement into consideration when he chose the upper and lower drive pulley's. I told him up front I wanted 4-6 lbs of boost. He supplied 53 and 55 tooth pulleys which, at best, would yield 3-4 pounds of boost in an overdrive (small pulley on top) configuration. He dismissed my concerns so I purchased a 59 tooth pulley from Nutech Racing. With the 55 on top and 59 at the crank, I'd get a 7.3% overdrive or around 5 lbs. of boost (confiirmed
6-lbs. via a boost gauge). Remember, engine displacement, static compression ratio, and pulley ratios will determine boost levels. There are limitations in order to run on pump gas without detonation.
By the way, 8mm tooth pulley's will handle greater loads than the older style 1/2" gilmer drives. My tooth counts and ratios are based on 8mm drives.
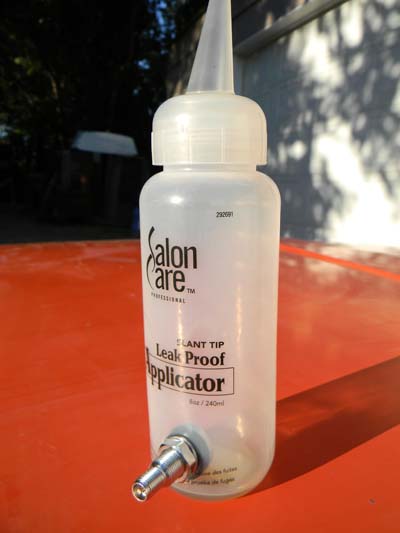
And finally, here's a little tip if you need to drain and fill a blower gear case:
Draining is easy - just pull one of the lower snout to gear case bolts with a container beneath to catch the oil. A section of plastic milk jug works well for me. Not all of the oil will drain out but most will and you'll be able to remove the snout or triangle gear cover if necessary.
Refilling with 90 weight gear oil (1 pint) through one of these bolt holes can be tedious. I picked up an applicator bottle from a beauty supply house along with a threaded valve stem found on custom wheels.
I used a steel rod or piece of tubing heated with a torch to melt a perfect hole in the bottle for the valve stem.
Once installed, a few pounds of compressed air from your air chuck will dispense the oil in about 30 seconds!
© 2013 JP Herrick Enterprises - All Rights Reserved
Site updated: January 2014